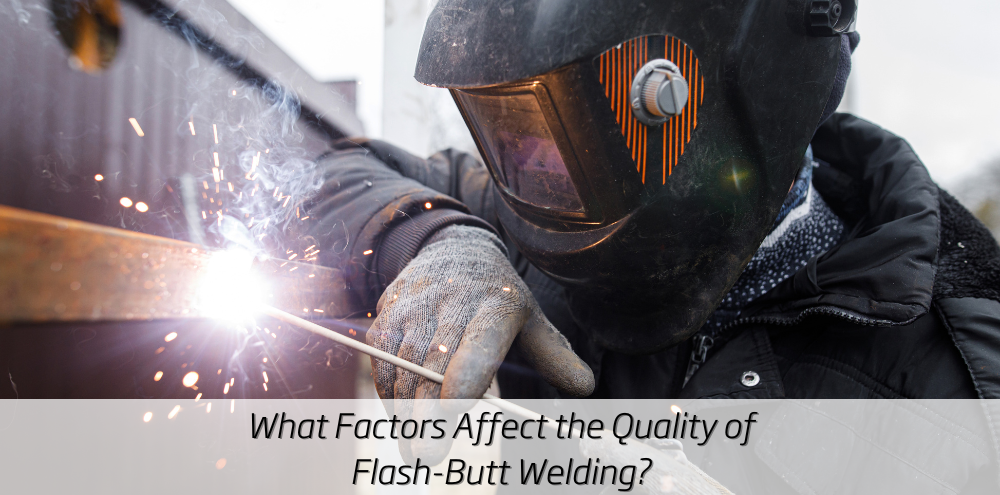
What Factors Affect the Quality of Flash-Butt Welding?
Flush-butt welding helps join two metal pieces. This technique uses electricity to heat the metals’ ends until they’re malleable. After heating, these metal ends are joined under pressure. Flash-butt welding provides numerous benefits. However, it also has some drawbacks worth considering before deciding if it is a perfect match for your project.
Several factors affect the flash-butt weld quality. They include:
Materials
When the parent material is highly inhomogeneous, several specific factors arise. Some examples include:
- Steels that have rolling defects or are heavily banded
- Metals containing longer stringer inclusions
The upset at the weld line can alter the fiber direction of the structure. This may result in reduced ductility. Also, hook cracks may develop.
Process Factors
Process factors also influence the output of flash-butt welding machines. Things like voltage and speed are carefully selected to provide sufficient heat build-up and excellent flashing action in the weld area. Too low heat can’t produce enough upset to achieve the best weld.
There’s a risk of creating inclusions and cratering in weld areas. This happens when the flashing is intermittent or coarse. It leads to flat spot flaws. The materials need to be softened sufficiently to allow for proper upset. And this is where flashing time settings become vital.
Overheating also affects a flash-butt weld quality. An overheated metal that isn’t well-forged during the upset process may be susceptible to embrittlement. A break-up may occur in this area.
After flashing, the current must be enough. This is especially vital during the upset’s first part. It allows the upset to be achieved fully. And doesn’t result in the overheating of the weld region. To trigger sufficient deformation, three key things must be set. They include:
- Upset distance
- Upset rate
- Upset force
When you properly set the upset distance, rate, and force, you’ll eliminate the contaminants and molten material from the surface of the joint.
High-Quality Rail Bend Testing Press
A high-quality rail bend testing press also determines the quality of a flash-butt weld. A rail bend testing press is essential for quality assurance. It offers precise measurements and testing for the safety and durability of rail. A rail bend testing press ensures the accuracy of your weld. And this means good quality flash-but weld.
When used properly, flash-butt weld can provide durable connections between two metal pieces. This technique is cost-effective compared to the likes of brazing and riveting. Remember, skilled personnel and a reputable equipment provider ensure a high-quality flash-but weld.
Read More: click here